Automate or Die
Automation is one of the main catalysts of today’s industrial evolution. With better and better automation processes comes ever-advancing industrial marvels, making ideas and concepts that were unimaginable a few years ago, common and widely used. But why is automation such a big deal?
by Péter Bohács, ECI Manager at Organica Water
As we progress beyond the industrial revolution, increasingly more processes (and more complex processes) are becoming automated. The automation trend ranges from check out cash registers at Tesco to the driverless metro system in Singapore. There is now serious research being conducted on automated road vehicles, and articles published on the eventuality of empty airplane cockpits; a frightening thought today for many. The truth is that automation reduces the room for human error and inneficiencies in response time, while built-in redundancy ensures safe operation.
For Organica automation is a key aspect in all of our references and for good reason. Our scope for any project is limited, yet we still must guarantee performance of our designs, including all of the OPEX advantages that come with implementing our solutions. We integrate advanced process knowledge into the automation systems, which enable the end user to operate the plant in an optimal way, without relying on continuous coverage by personnel.
With real-time monitoring instrumentation, the system never misses any sign of change in the process and with control loops it automatically adapts to the change of the input parameter. It also ensures full safety in operation thru these interlocks. Additionally, the system ensures that the wear of the duty and stand-by equipment is balanced. It can be also used to remind operators of regular maintenance and will notify an operator when their intervention is required.
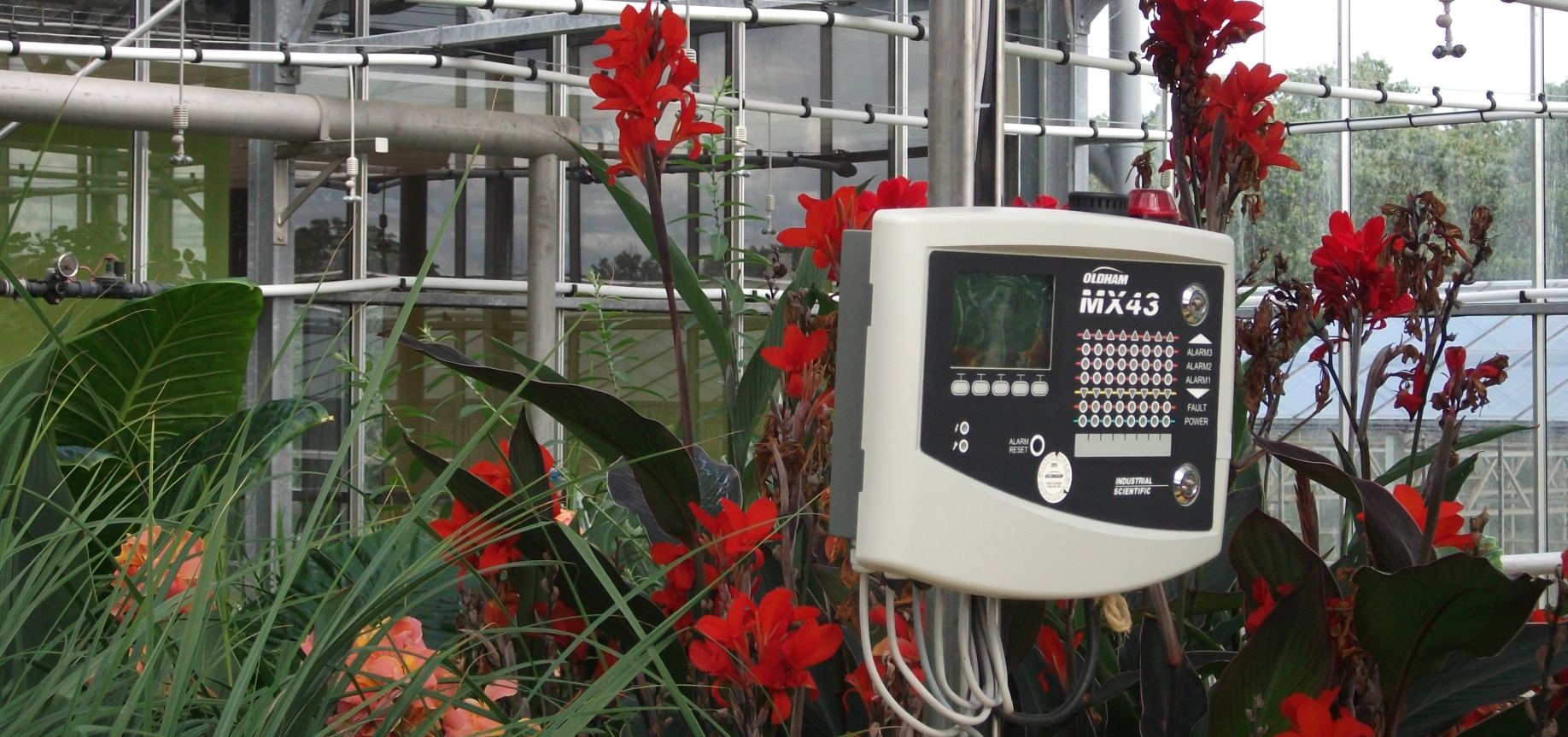
Instrument Board South Pest WWTP
For higher-capacity plants a redundant automation system can be integrated and used to further ensure safe and efficient operation. Further, multiple control philosophies can co-exist in the system and their application can be selected either manually or automatically, for example seasonal changes. Emergency and fall-back strategies can be programmed into the system and these can be initiated automatically: people forget procedures that they do not execute regularly or they can be slow to react to a situation that can cause serious damage. An automated system however will always be watching in situations such as this.
Automatic control loops however, are only as good as the input data fed to them: higher levels of automation usually require a higher level of instrumentation which can increase CAPEX. On the other hand the cost of this instrumentation can be recovered by the more efficient operation of the plant, both in power consumption and in work scheduling (example: two level switches in a sludge storage tank do not give much help in determining when to plan the start of dewatering, but an ultrasonic level transmitter can accurately tell how much sludge is in the tank and from the rate of increase it can be predicted when it will reach the amount for a most optimal run.)
Lastly, the automation system records everything that is happening in the plant and can store it for years, making record-keeping easier. The collected data in the system is avaliable for statistical calculations or process evaluation calculations can be easily run on their basis, tracking long term performance and any changes in water quality influent trends.
While operating complex infrastructure that serves the vital functions of sanitation and in many cases water reuse for years on end without stop, automation helps us to sleep better in the end.